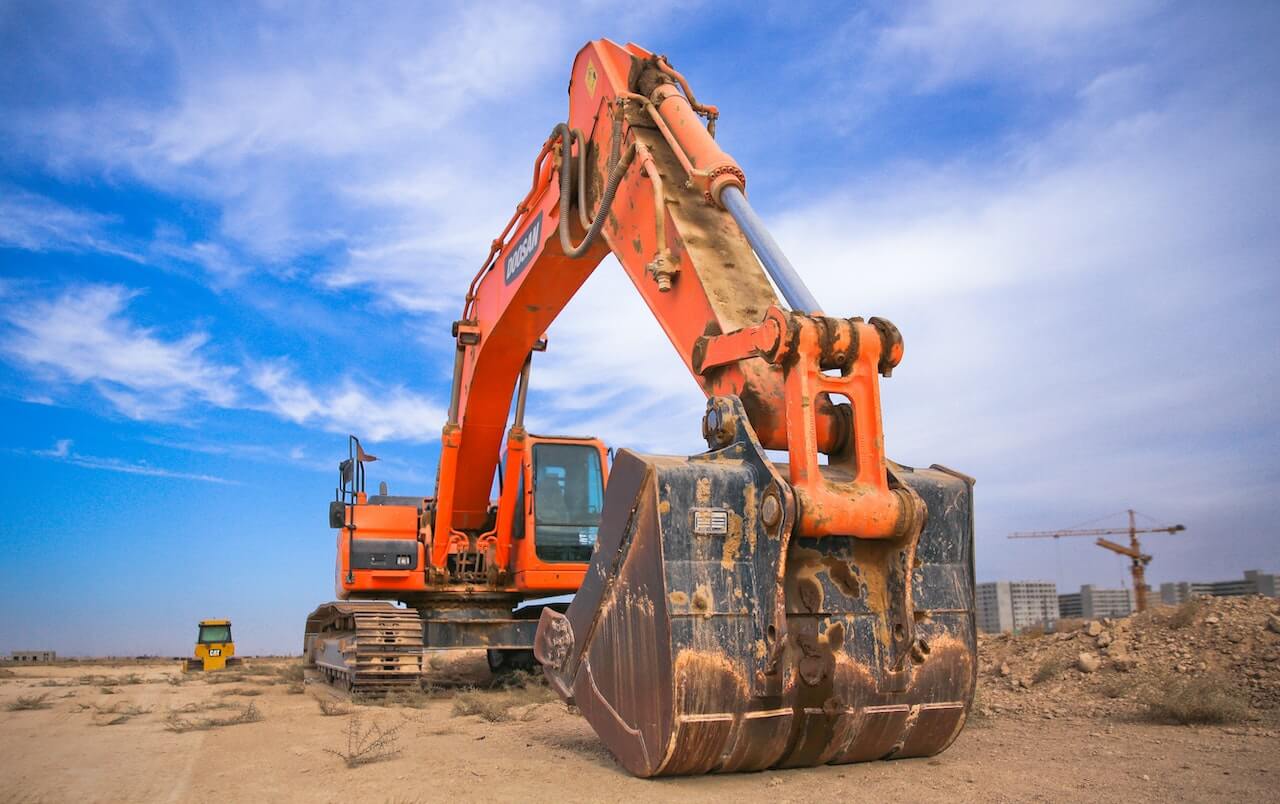
この記事では、「離散シミュレーションに基づく、産業機器レンタル業務の改善」という論文について 紹介します。こちらの論文では、在庫不足を減らすために三つの業務改善方法を提案し、それぞれの効果的を離散シミュレーションによって定量的に評価しています。
シミュレータを作るのは少々手間がかかりますが、業務改善内容のインパクトを定量的に評価したい場合には有効な手法です。 シミュレーションによってどのような分析が可能なのかについて興味がある方はぜひご覧ください。
紹介する論文
Operational improvement of an industrial equipment rental system using discrete event simulation
1. 論文の概要
論文では、産業機器レンタル事業における「貸出し在庫不足(失注)」が発生する問題に対して下記三種類の業務改善を思案し、 それぞれの効果を離散シミュレーションを用いて定量的に評価しています。
- 在庫数を増やす
- 在庫不足を減らすための最も直接的な方法。
- 返却後処理時間を短くする
- 変客後の処理時間を短くして在庫回転率を上げる。
- 返却処理を行う機器の順番を変える
- メンテナンス施設に到達した順に処理を行うのではなく、有効在庫数が少ない商品を優先的に処理する。
2. 事業特性と、構築した離散シミュレータと詳細
論文で取り上げた産業機器レンタル事業者は、表 1 の商品を取り扱っています。
商品 | 在庫数(個) | 一ヶ月あたり平均需要(個) | 平均レンタル期間(日) |
---|---|---|---|
フォークリフト | 147 | 159 | 18 |
コンプレッサー | 44 | 32 | 16 |
昇降機 | 539 | 740 | 13 |
発電機 | 312 | 153 | 23 |
また、実際のレンタル業務の流れ図は以下のとおりです。
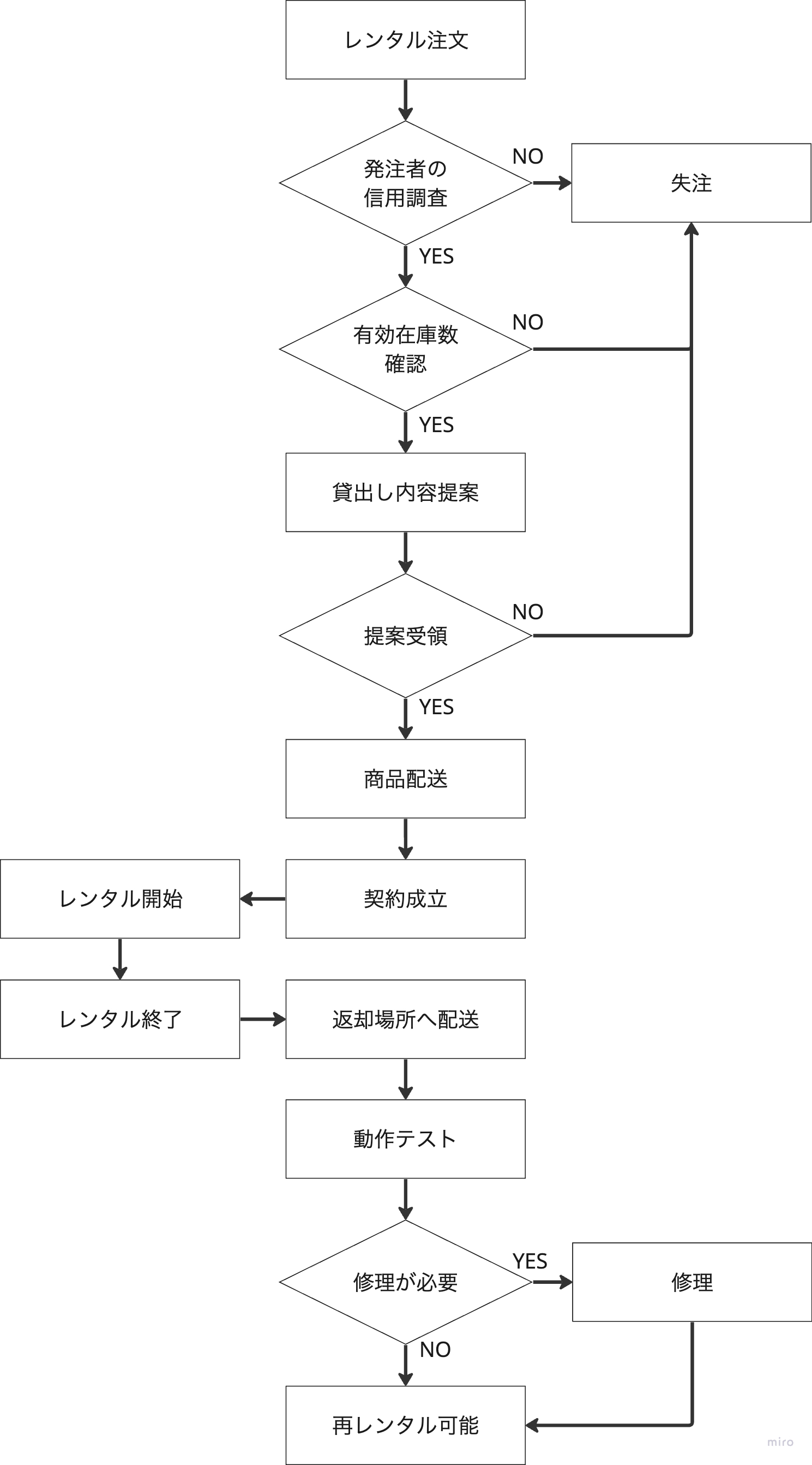
特筆すべき点として、商品返却後は動作テストを行う必要があります。 論文で取り上げている事業者では、ほとんどのケースで問題なく動作テストは完了しますが、約 12%のテストにて問題が発生しています。 この場合、商品はメンテナンス施設に送られ、修理が行われます。修理には平均 5 日かかります。 また修理作業にも一定のキャパシティが存在し、メンテナンスが必要な在庫数が増加すると、修理待ちとなる在庫が発生する場合もあります。
シミュレーターは上記の流れ図をもとに構築されています。注文の発生タイミングや、返却タイミング、レンタル期間などの不確実性が存在する パラメータについては、実際の注文データから確率分布を推定し、それをもとにシミュレーションを行っています。具体的なパラメータと 確率分布については、論文の Table 2 を参照してください。
不確実性を考慮するために、75 回の確率的なシミュレーションを実行し、その平均を用いてシミュレーションの結果としています。 各シミュレーションでは 260 日分の期間をシミュレートし、その期間中の在庫利用率や失注数を得ます。
3. 業務改善効果の感度分析
まず、表 1 の在庫数をもとにシミュレーションを行った結果が表 2 です。 シミュレーションの結果から特筆すべき点として、260 日を通してフォークリフトと昇降機はそれぞれ 505 個と 2349 個分もの注文を失注しています。 これは表1から推測するに、それぞれの在庫数が月間需要を下回っているために発生していると考えられます。
商品 | 在庫利用率(%) | 失注数(個) | 失注率(%) |
---|---|---|---|
フォークリフト | 94.1 | 505 | 3.88 |
コンプレッサー | 76.8 | 24 | 0.18 |
昇降機 | 94.2 | 2349 | 18.04 |
発電機 | 67.8 | 4 | 0.03 |
そこで、以降のセクションでは改善の必要性が高いフォークリフトと昇降機に着目して、業務改善案の効果をシミュレートします。
注文が多いほど在庫利用率は高くなりますが、それは顧客のもとに商品を貸し出すことになるので 有効在庫数は減少します。そのため他の顧客からの注文に対応できず、失注する可能性も高くなります。
各指標のバランス目標をどの程度に設定するかは、ビジネスの性質によって異なります。
例えば大型の商品を扱う事業者の場合、有効在庫数が低いことは倉庫のスペースを有効活用できていないことを意味するので、 在庫利用率も失注率と同様に重視する必要があるでしょう。
3.1 在庫数を増やした場合
フォークリフトと昇降機の在庫数を基準(表1参照)から増やした際に、 在庫利用率がどのように変化するかをシミュレーションによって確認した結果が以下の表になります。
商品 | 失注数 (変更前) | 失注数 (在庫数:+25%) | 失注数 (在庫数:+50%) |
---|---|---|---|
フォークリフト | 505 | 260 (↓ 改善) | 147 (↓ 改善) |
昇降機 | 2349 | 2431 (↑ 悪化) | 2461 (↑ 悪化) |
商品 | 失注数 (変更前) | 失注数 (在庫数:+25%) | 失注数 (在庫数:+50%) |
---|---|---|---|
フォークリフト | 505 | 549 (↑ 悪化) | 583 (↑ 悪化) |
昇降機 | 2349 | 1554 (↓ 改善) | 872 (↓ 改善) |
期待したとおり、それぞれの在庫を増やすことで失注率が改善しています。 しかし、意に反してフォークリフトの在庫数を増やすことで昇降機の失注数が増加しています。
これは、第2章で紹介したとおり、 在庫数の増加によってメンテナンス待ちの在庫が発生したことによる有効在庫数の減少が原因と考えられます。
この結果から、在庫を増やすという投資判断を行う際には、 失注率の改善効果とメンテナンス待ち在庫による有効在庫数減少のバランスを考慮する必要があると言えます。
3.2 返却後処理時間を短くする
次に、ボトルネックとして考えられる返却後処理時間を短くすることで、失注数を改善できないかシミュレーションしました。 その結果が表 5 になります。
商品 | 失注数 (メンテナンス 5 日) | 失注数 (メンテナンス 3 日) |
---|---|---|
フォークリフト | 505 | 467 (↓ 改善) |
昇降機 | 2349 | 2175 (↓ 改善) |
こちらは 3.1 と異なり、どちらの商品においても失注数を改善することができることがシミュレーションによって確認できました。 フォークリフトの失注数は 505 個 から 467 個、昇降機は 2349 個から 2175 個にそれぞれ 10% 程度改善しています。
しかし、現実的にメンテナンス時間の削減は新たな設備や人員の投資を必要とする難しい課題です。 そのため次のセクションでは、メンテナンス処理を行う順番を整理することで、極力投資コストをかけずに失注数を改善する方法を検討します。
3.3 返却処理を行う機器の順番を変えた場合
論文で取り上げている事業者は、メンテナンス場に届いた商品を順番に処理していく、いわゆる FIFO(先入先出) 方式で処理を行っています。 そこで、需要の高い商品は優先的にメンテナンスを終わらせられれば、メンテナンス中から有効在庫に戻る時間が短縮され、結果的に失注数を改善できそうです。
優先順位付のアイディアとしては以下のようなものを採用しました。
まずを、商品に関する「有効在庫数/総在庫数」として定義します。これはいわゆる有効在庫割合です。 そしてメンテナンス処理を、が低い順に処理を行うことにします。
上記のアイディアをシミュレートした結果が以下の表になります。
商品 | 失注数 (FIFO 方式) | 失注数 (方式) |
---|---|---|
フォークリフト | 505 | 476 (↓ 改善) |
コンプレッサー | 24 | 21 (↓ 改善) |
昇降機 | 2349 | 2229 (↓ 改善) |
発電機 | 4 | 3 (↓ 改善) |
論文のケースでは、他の商品の失注数に悪影響を与えることなく、フォークリフトと昇降機の失注数を改善することができています。
4. まとめ
本記事では、論文「A Simulation Study of the Impact of Rental Equipment Maintenance Policies on Customer Service」を紹介しました。 論文では離散シミュレータ上で業務改善アイディアを検証し、そのインパクトについて失注数や在庫利用率を指標として評価していました。
論文で紹介されている以外にもシミュレータの利用価値は多くあると思います。 例えば3.1のように、在庫購入時にはシミュレータで「楽観ケース」や「悲観ケース」をシミュレートし、 在庫購入リスクを評価することが手軽にできると思います。